A bit addictive so I made another - wanted a turquoise one
all finished except made it a bit too long so I'll have to reduce it by about 6 inches but otherwise not too bad
got carried away while watching TV and just kept sewing the beads onto the leather - these are smaller beads than the last ones (around 5mm) but I think I can go smaller - I'll find some 4mm next and see
Wrap Bracelet
I keep seeing these wrap bracelets in ads on Facebook as well as my daughter wants one and asked if I could make one
tripped up to the studio to find leather cord, some nymo thread, needles and some beads - now I have a ton of beads but of course not the ones I need - although I did find some 6mm glass coloured that I thought I'll just do a prototype and see how hard it is
You use the ladder stitch - here is a tutorial http://www.limabeads.com/Learning-the-Ladder-Stitch-T33
The tutorial I followed:
Lots of tutorials on google - not very hard
I like this one now the best from Rings N Things
http://www.rings-things.com/blog/2011/03/08/how-to-make-wrapped-leather-bracelets/#.UwuwDPk7uM4
followed a tutorial on the web - I may have used a bit larger than I should have for beads ? not sure - they said 6 mm - not happy with the way they did the ends and found another I would prefer to follow so the next one will be better and I want 5 wraps in the end
tripped up to the studio to find leather cord, some nymo thread, needles and some beads - now I have a ton of beads but of course not the ones I need - although I did find some 6mm glass coloured that I thought I'll just do a prototype and see how hard it is
You use the ladder stitch - here is a tutorial http://www.limabeads.com/Learning-the-Ladder-Stitch-T33
The tutorial I followed:
Lots of tutorials on google - not very hard
I like this one now the best from Rings N Things
http://www.rings-things.com/blog/2011/03/08/how-to-make-wrapped-leather-bracelets/#.UwuwDPk7uM4
followed a tutorial on the web - I may have used a bit larger than I should have for beads ? not sure - they said 6 mm - not happy with the way they did the ends and found another I would prefer to follow so the next one will be better and I want 5 wraps in the end
found my button stash ! and used a whole 1 button up
The torch is going on this week - got my new Brent Graber DVD for Hearts
I cant wait - Ill have to be sure I have some boro ready cause I'm going to watch my dvd tonight and get ready

Im in the mood to make hearts - lots of hearts

Im in the mood to make hearts - lots of hearts
More , copper/brass Etching
And got started early this morning so I can do three batches (if I really wanted to go gung ho I'd bring out the second hot plate and dish - which may happen this week so each night I can keep making)
1st batch was three plates while I prepped for 2nd batch
2nd (washers and one plate) and 3rd batch (3 plates) (need to be done by 2pm to meet my daughter and grandchildren for dinner)
finished 2nd batch and had one plate in the solution
final batch is 3 more plates
starting to accumulate cleaned pieces - used acetone to clean off the left over adhesive on the backs of the pieces (this tape seems to be great as it does not seem to leave as much on it ) and it takes off the staz on - then used the dremel with split mandrel and 220 sandpaper - takes off the edges and smooths the surface (will sandblast the plates and small pieces to get them clean inside the etched depressions)
Not being in the studio really is making things slow - cant just turn around and use my stations - have to trek through the snow and cold - cant wait for spring
Etched Sheets out of the Etch
Have the mustaches washers and now the sheets out of the etching solution
Will spend the day Monday (holiday here) and see if I can do all the washers , small mustaches and seahorses and get a bunch of stuff done
will accumulate and then clean all at once
Will spend the day Monday (holiday here) and see if I can do all the washers , small mustaches and seahorses and get a bunch of stuff done
Out of the Etch
After about 1 hour or so
its getting to be a good etch
Hour and a half taking it out
get those gloves on - this stuff stains your hands - up to now I can work without touching the solution but just in case I like to wear the gloves
I unstick from the sides drain what I can and just place onto some paper towel face up so it doesn't stick
make a dish of water and baking soda to clean them off and to stop the etch
than I rinse and put them into another clean bowl of baking soda and water
now they are sitting and I will seperate them and clean them up
In the mean time I'll put in another batch for today
of the 3" x 4"
Stamping Copper for Etching- refresher
In an effort to work my way up to doing the 3" x 4" squares of copper I need to set up for stamping and etching so I thought I'd start with some smaller items to get working again
I pulled out my stamps (which had been sitting frozen at the shed and covered in staz-on - I forgot to clean off) took out some acetone and cleaned up using the acetone and a toothbrush and paper towel
I pulled out my stamps (which had been sitting frozen at the shed and covered in staz-on - I forgot to clean off) took out some acetone and cleaned up using the acetone and a toothbrush and paper towel
These are my original stamps when I first had them made so they have lasted through hot, cold - lots of acetone cleaning and stamping and are still in great shape
(stamps can be purchased at my Etsy shop (see top left side bar))
I cleaned my copper with acetone
today are moustaches and brass washers
then I use the staz-on to dab onto the area I am using to stamp onto the pieces
You need to stamp quickly as it does dry quickly
dont push the stamp down too hard - you only want to the surface lines to be covered
Place the piece clean side down (be sure to hold by sides as you dont want the oils from your hands to get onto the piece )
DONT PUSH HARD
because its rubber stamp it will spread and smear
I usually hold down with one finger and lightly go around the edges to ensure it meets the stamp
I'll keep the one finger down with a bit of pressure and pull up the piece all in one pull
I find some of the odd size and shapes are a bit harder to work with - dont worry if you get any on the backs - it comes off later
Let them dry
Now I have to set up my etching system
Hot plate, cookie sheet with aluminum foil, glass cake pan
I put in some etching chemical (ferric Chloride)
I dont put a whole bunch, just enough that I can have the pieces sit on the surface
I turn on the hot plat - ONLY TO WARM- too hot and it affects the solution and the etch
Now to get the dried pieces ready to be put into the etc.
I picked up some 3" wide packing tape - normally I have 2" but sometimes I have items that are odd shapes and they stick out or if I want to put a bunch together the 3" works great
I check to see how many I can put on the tape by pulling out one of the nail files that I use as a support to see the length
Place all your pieces with the stamped side face down
and put the tape over the entire group (I fold the ends to be able to pick up easier) note I have some staz-on on the back of my pieces - dont worry it all comes off later
I use my finger to burnish the tape to the metal pieces
then I place one of the nail files for support (so it does not bow in the etching solution) keeps it flat and straight
then another layer of tape to hold the file on top and to keep the etching solution from the file (most of the time)
next pick up by the end and make sure it all stays together
I lay it lightly on top of the etching solution and stick the ends to the sides of the glass
because this tape is wider I am only getting 3 strips in at a time where I get 5 usually with the 2"
so now because this is fresh etching solution I'll check at 1 hour - 1-1/2 hour and 2 hours
as it etches to see how deep the etch is
GROW YOUR BLOG GIVE-A-WAY WINNER IS >>>>>>>>>>>>>>>>>
Andrea Ostapovitch
Congratulations to Andrea for winning the Grow Your Blog Give-A-Way
I had a great turn out for the Give-A-Way and for Grow Your Blog
Keep returning as I'll always have some new step by Steps and other crafty ideas you may want to try
Again thank you to you all
Andrea I'll be in touch to get your mailing address or you can email me at dread@deborahread.com
and put winner in the subject line
Grow Your Blog Give-A-Way - will be ending on Sautrday the 15th
Will pull a name on Saturday morning for a winner for the Grow Your Blog Give-A-Way
Dont miss out on the copper etched pendant - just find the thread (see side bar for quick link ) and just leave a comment
(here is a link as well ) http://deborahreadcom.blogspot.ca/2014/01/grow-your-blog-jan-25-2014-special-give.html
would love you to join my followers so I can grow my blog up the the 150 I would like to grow to this year (or more)
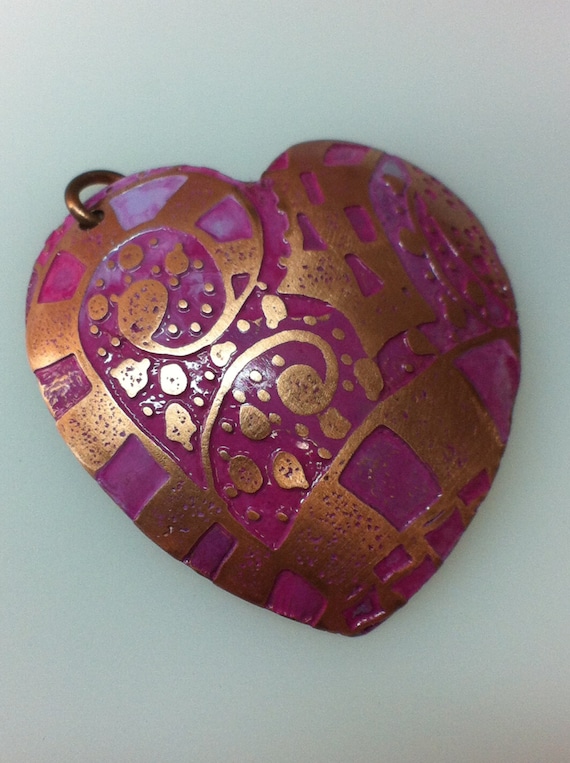
Dont miss out on the copper etched pendant - just find the thread (see side bar for quick link ) and just leave a comment
(here is a link as well ) http://deborahreadcom.blogspot.ca/2014/01/grow-your-blog-jan-25-2014-special-give.html
would love you to join my followers so I can grow my blog up the the 150 I would like to grow to this year (or more)
Flattening and cleaning copper sheet for etching
tonights project is to flatten the 3 x 4 sheets for etching
Even when you use the shear or scissors you get a bit of a curl and bends in the copper
you want it as flat as you can to put your design on so its even
I use my two steel blocks and a hammer - to tap on this way you dont get hammer marks on the soft copper and because its soft it flattens the piece out
I position it in quarters
Even when you use the shear or scissors you get a bit of a curl and bends in the copper
I use my two steel blocks and a hammer - to tap on this way you dont get hammer marks on the soft copper and because its soft it flattens the piece out
I position it in quarters
and tap tap tap
takes away the curl of the edge and levels it all out
all nice and flat and ready for cleaning
I got some nice hot water and soap and then put them in to cut the oils
as I pulled them out and gave them a squirt of windex and cleaned them up being careful to hold them by the sides so any oils from my hands did not get on the clean surfaces - oils can make the resist not adhere to the metal surface
cleaned and ready for the resists
I will wrap up to keep any dirt or oils from getting on them till I am ready to apply (hopefully tomorrow)